关于我们
年轻朝气的团队、专业严谨的态度、专注努力的精神,赢得了客户的信赖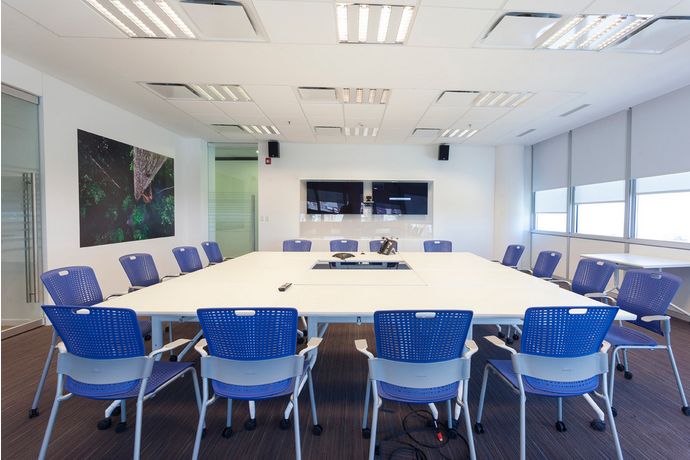
上海万蕴企业管理咨询有限公司 上海万蕴企业管理咨询有限公司是一家专业咨询机构,专业TS特种设备生产许可证咨询(包括:压力管道元件制造许可证、压力管道安装许可证、压力管道设计许可证、压力容器制造许可证、压力容器设计许可证、锅炉制造许可证、锅炉安装许可证、起重机械许可证、起重机械安装许可证、电梯制造许可证、电梯安装许可证、游乐设施制造许可证、安全附件制造许可证、厂内机动车辆制造许可证、安全附件许可证等);LA安全标识认证咨询、CCC认证咨询、节水认证咨询、三标体系认证咨询等认证咨询服务; 我们的服务范围涵盖石油、化工、工业品、汽车、建筑等重要行业。拥有专业齐全、阵容强大的咨询师、培训师队伍。通过...
查看更多>> 新闻中心
关注我们,了解最新最全企业相关资讯232022-11
1 任职条件1) 从事压力容器设计、校核、审批的人员应当具备相应专业设计能力,能够正确使用压力容器设计相关的软件,由鉴定评审机构通过理论知识考试、设计答辩等方式, 对其进行压力容器设计专业能力评价。2) 理论知···
232022-11
设计单位准备的试设计文件应当覆盖其申请范围,并且具有代表性。试设计文件数量及要求见表 C-1。试设计文件不得用于制造和安装。表 C-1 试设计文件数量及要求许可子项目试设计文件数量(注 C-2)备 注压力容器分析设计···
232022-11
1) 参照本规则附件 M 的要求 ,设计单位应当建立至少包括文件和记录控制、合同控制、设计控制、不合格品(项)控制、人员管理、质量改进与服务、执行特种设备许可制度等控制要素的质量保证体系 ,并且能够有效实施 ;编···
232022-11
1) 换证提供的实际产品的设计文件应当覆盖设计许可范围,并且具有代表性,无设计业绩时,按照首次申请取证的要求准备试设计文件。2)申请本规则 3.6.3.2 条“自我声明承诺换证”的,相应级别的设计审批人员变化率不大···
232022-11
《压力容器许可证-压力容器制造许可证-压力容器设计许可证-压力管道安装许可证》
232022-11
《压力管道元件制造许可证-压力管道安装许可证-锅炉许可证-压力容器许可证》特种设备生产许可证许可程序: 许可程序包括申请、受理、鉴定评审、审查与发证。1 申请1.1 一般要求申请采用网上填报的方式。申请单位应当···